Research & Development
To remain a leader in 3D and contactless measurement as well as quality control, we have to constantly look for new technologies and innovate.
Our R&D unit has for major goal to develop systems meeting customers’ requirements but also to anticipate and foresee their future needs. This includes feasibility and industrialization studies.
For the past few years, we have been working on several big research projects. Major industrial companies and clusters were involved in those collaborative projects:
TOCATA: OPTICAL TECHNOLOGY COUPLED TO AUTOMATED TOPOLOGICAL ANALYSIS
The aim was to develop a new system for the control of aerospace part after machining by combining numerous NDT.
- - Green technology to replace dye penetrant inspection
- - Process fully automated
- - Traceability of the defects warranted
- - Defect characterization thanks to three inspection methods :
- Optical detection
- Eddy current inspection
- Thermal imaging analysis
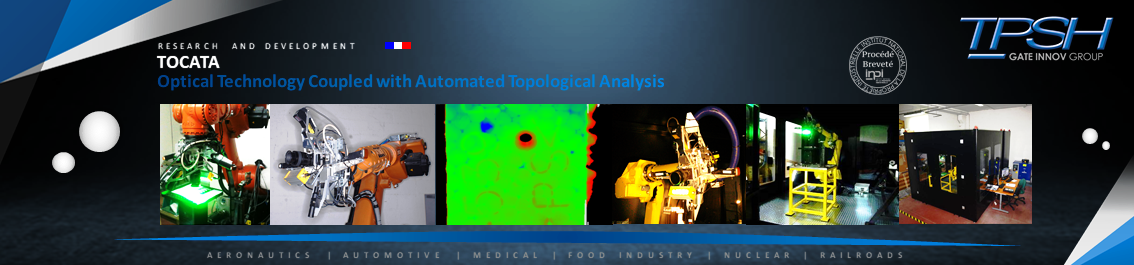
Photo illustration of the measuring head for the TOCATA project.
FALAFEL: Additive Manufacturing via Laser Processes and Electron beam
- - Additive manufacturing technology (DMD & SLM) for large aerospace parts,
- - Working on aerospace composite material,
- - Automation of the manufacturing cycle,
- - Real-time correction of the manufacturing deviation,
- - Monitoring of DMD and SLM machines,
- - Manufacturing traceability,
- - Storage of selective physical and geometrical parameters of the molten bath,
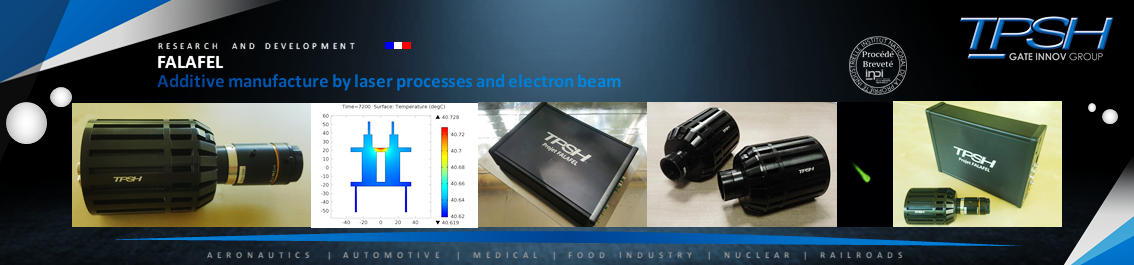
Photo illustration of the camera for the FALAFEL project.
PAM-PROD: ADDITIVE MANUFACTURING PROCESSES – PRODUCTIVITY (2019)
TPSH is in charge of the real time MAG LASER and CLAD process control to check the conformity of future parts manufactured by the hybrid machine. The control process will be done with the TCAM128-65, a multi-spectral, SWIR infrared visible camera, 100% developed by TPSH.
In the PAMPROD project, TPSH is in charge of the development of the control, monitoring and real time regulation part of the process. For this part, TPSH is developing a network of infrared sensitive cameras allowing :
- - To follow in real time the parameters of the melting baths,
- - Analyze the conformity of production parameters,
- - Send regulation or drift signals in real time,
- - To regulate in real time the machine parameters to ensure the good conformity of the manufacture by the means of a ” merging box ” allowing the real time connection has 1,5ms with the automaton SIEMEN 840D of the manufacturing machine.
The PAMPROD project is the economical solution to manufacture large parts, up to 5m in additive manufacturing. The machines are equipped with a hybrid additive manufacturing solution, combining powder and wire deposition. The patented technologies will allow real-time monitoring of the deposits at the level of the fusion bath thanks to our visualization system combining cameras and a HMI. A thermo-mechanical simulation, before the part is launched in production, will ensure the perfect conformity of the part.
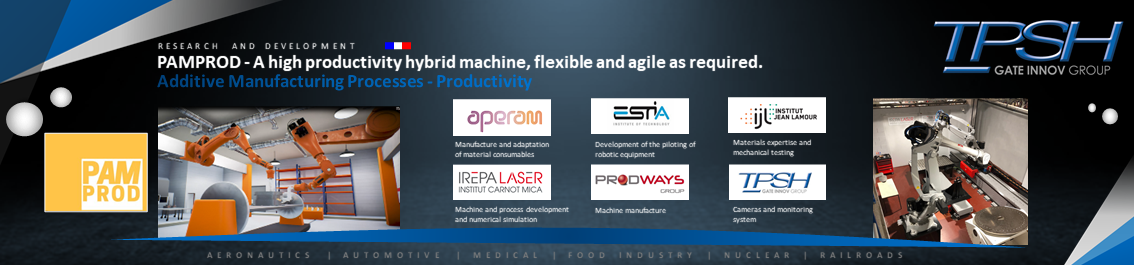
Visual illustration of the PAMPROD project.
Find news about the PAMPORD project on LinkedIn To learn more about the machine, click on the link.